Preface
The Mount Allison Fine Arts and Sciences Joint Health and Safety Manual outlines general responsibilities and procedures for the faculty, students, staff, and visitors of the department. The guidelines described are intended to help identify and evaluate hazards to minimize the risks that can arise in a laboratory or studio environment. Compliance with the manual will help promote safe laboratory and studio practices and prevent the risk of injury and incidents in the workplace.
Available safety training
WHMIS (mandatory for people using studio and lab spaces)
Available on Moodle as a self-enrolled class called “WHMIS Lab Safety Training” under “My courses > Safety Training & Lab Techniques”.
Cryogenic training (mandatory if working with cryogenic material)
Contact Philip Cormier (pcormier@mta.ca) and access the Cryogenic Plant Safety Manual (PDF) available on Moodle under “All courses > Safety Training & Lab Techniques > Lab Safety Training”.
Autoclave training (mandatory if working with autoclaves)
Contact Shelley LeBlanc (shleblanc@mta.ca).
Compressed gas training (mandatory if working with compressed gas)
Contact Chris Vogels (cvogels@mta.ca) and access the Compressed Gas Manual (PDF) on Moodle under “All courses > Safety Training & Lab Techniques > Lab Safety Training”.
Lab-specific equipment
Your supervisor is required to train you on the safe operation of equipment specific to their laboratory. Before using any equipment for the first time, or if you have questions about the operation of equipment you have used before, contact your supervisor.
Health and safety committees
For more information about University Health and Safety Committees or the Fine Arts and Sciences Joint Health and Safety Committee, contact the FASJ Health and Safety Committee (fasjhsc@mta.ca).
Resources and definitions
New Brunswick Occupational Health and Safety Act (NB OHS Act)
New Brunswick’s Occupational Health and Safety Act (NB OHS Act) can be found on the WorkSafeNB website and outlines the duties of employees and employers. Many definitions and contents in this manual are drawn from it (S.N.B. 1983, c. O-09.2, sect. 1).
Employee
An employee is defined as:
- A person employed in a workplace.
- A person in a workplace for any purpose in connection to the workplace, such as a volunteer or unpaid, on-the-job learner.
In a research laboratory, employees include the people (often called students) who are working outside of the classroom, for pay (e.g., research assistant), or as volunteers.
In a teaching laboratory, employees include teaching assistants but not the students who are attending the lab portion for class credit.
Further guidance on the interpretation of employee under the NB OHS Act is available at WorkSafeNB.
Employer
An employer is defined as a person who employs one or more employees or the person’s agent. In the context of a research laboratory, employers include faculty who have hired people to work in their research laboratory space.
Supervisor
A supervisor is defined as a person who is authorized by an employer to supervise or direct the work of the employer’s employees.
Supervisors at Mount Allison can be faculty, staff, or someone designated by faculty/staff, who manage employees in a laboratory or studio context.
Principal Investigator (PI)
A faculty member or a research scientist responsible for managing, planning, safety tracking and conducting sponsored research at Mount Allison through research grants, public service projects, etc.
Visitors
A person who is not granted permission to work in a laboratory or studio is a visitor of that space. Examples of visitors include parents, campus tours, and friends.
Laboratory
A laboratory is a space equipped to carry out scientific experiments. There are two types of laboratories, a teaching lab and a research lab.
As part of academic course work, science students carry out experimental procedures in teaching labs instructed by a laboratory instructor and/or professor.
Research labs are laboratories assigned to principal investigators (PI), these labs perform advanced laboratory activities for research and are a place to train individuals on such practices.
Studio
A studio is a space equipped to pursue and create art.
Hazardous product
An agent that could be encountered in a chemical, radioactive, physical, or biological form and that could put someone’s health or safety at risk if exposed.
Personal Protective Equipment (PPE)
Equipment worn by individuals to reduce exposure risks to hazards that could injure their health. Hazards that may result in injury or illness include contact with chemical, physical, mechanical, electrical materials, etc.
Unattended procedures
Equipment or processes that operate in the laboratory with a person overseeing the procedure. This includes situations where no personnel are physically present, and those where someone is present but they are unaware of the occurring procedure.
Incident
An event causing an injury or an occupational disease.
Near miss
An event that could have been prevented, which had the potential for causing an injury or an occupational disease but did not.
Safety manual
1. Employee rights
Your health and safety rights when taking part in laboratory procedures are the following:
Right to know
The right to receive information, instruction, and training needed to do your job safely, including information about potential hazards in your workplace. Information can be in the form of safety data sheets (SDS), labels, and procedures for safe work and practice. Instructions can be given by a supervisor, employee, or instructor and can be provided verbally or in writing.
Right to participate
The right to take part in matters that can affect your health and safety, including taking part in training, offering suggestions to reduce risks, and reporting hazards to your employer or supervisor. It is a requirement by the NB OHS Act that employees report any health and safety concerns and that the employer receiving the information act on the issue rapidly.
Right to refuse
The right to refuse work if you believe it is unsafe to you or others, following an obligation to report any problematic or dangerous situation. For legal refusal of work and for productive actions to be taken, follow the flow chart.
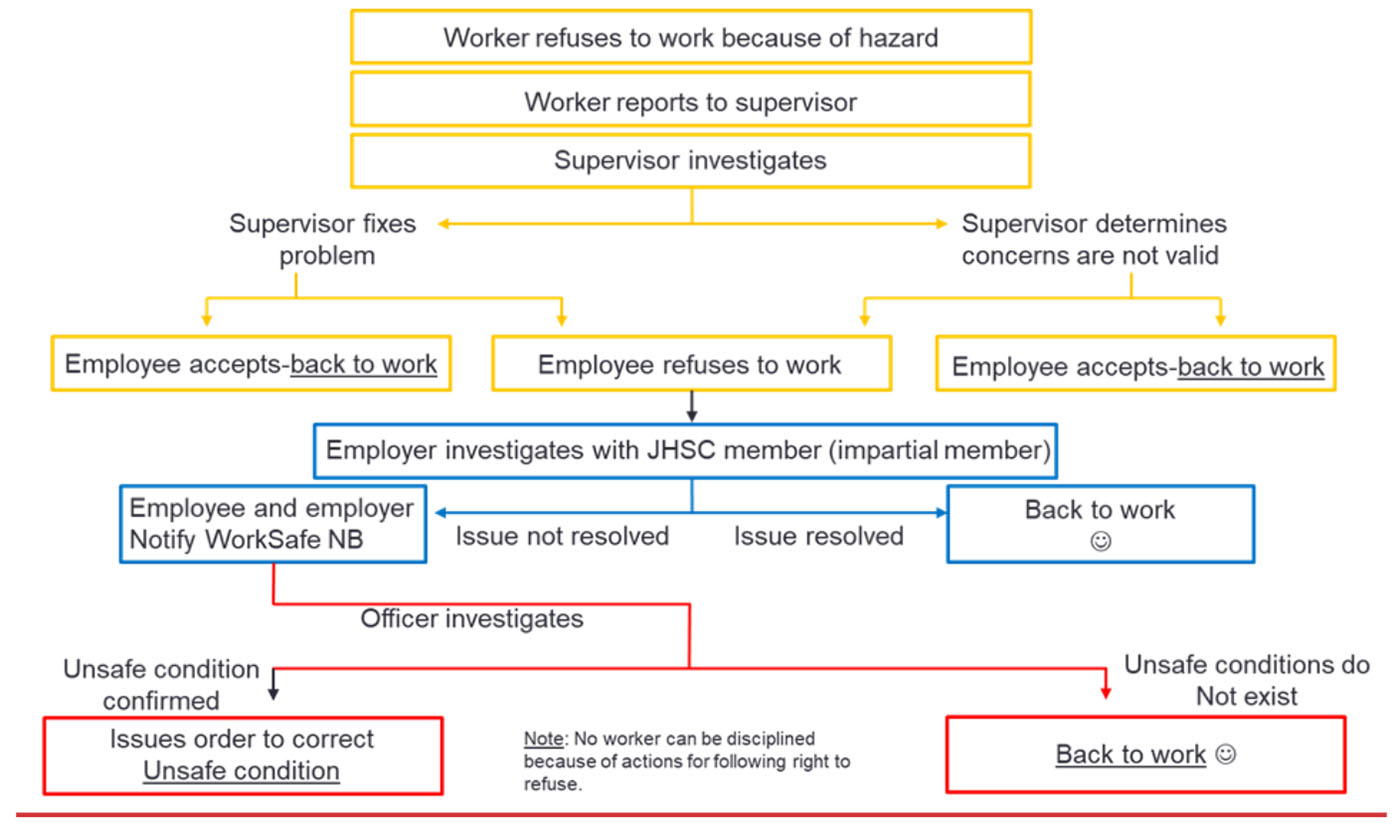
Additional description of the steps to be taken are outlined below:
- Inform your supervisor of the concern, the supervisor must act on the concern or provide you with an explanation of why they disagree on the matter.
- If you deem your supervisor’s response unsatisfactory, you may report your concerns to the Joint Health and Safety Committee (fasjhsc@mta.ca). An investigation will be conducted and if appropriate, effective measures will be recommended to your employer.
- If you are unsatisfied with the actions of the Joint Health and Safety Committee, a health and safety officer from WorkSafeNB may be contacted.
No worker can be disciplined because of actions taken for following right to refuse.
It is strongly advised that the employee document their concern and keep track of who they have spoken to and any outcome from conversations.
For more information on employee rights, refer to the NB OHS Act.
2. Responsibilities
It is the responsibility of all individuals entering a laboratory or studio space to follow all operating procedures, use all required PPE, attend necessary safety training, and report incidents, injuries, and hazards. This ensures one’s own safety, the safety of others and the environment. Specific responsibilities based on role are presented below.
Employer responsibilities
Employers must take every reasonable precaution to ensure the health and safety of their employees. This includes:
- Ensuring that all instrumentation, machinery, and equipment are in good working order.
- Providing all necessary personal protective equipment.
- Familiarizing your employees with all workplace hazards, and training employees on the safe use, handling, storage, and transportation of equipment and materials.
- Immediately reporting all near misses and incidents to JHSC (fasjhsc@mta.ca) and HR (hr@mta.ca).
- Developing appropriate Standard Operating Procedures (SOP) as necessary.
- Ensuring all workplaces are sufficiently and competently supervised.
- Designating substitute supervision in the absence of the laboratory supervisor.
For more information on employer responsibility, refer to WorkSafeNB.
Supervisor responsibilities
Supervisors must take every reasonable precaution to ensure the health and safety of their employees. Supervisors oversee lab safety, and their responsibilities include, but are not limited to:
- Setting up appropriate warning and cautionary signs in the laboratory and providing appropriate PPE for use. This includes the Emergency Contact Information sheet (PowerPoint template), which should be filled, printed, laminated, and posted behind the corresponding lab door.
- Maintaining inventory of hazardous products in the lab, and a set of up-to-date SDS that is readily accessible to all laboratory employees.
- Inspecting emergency equipment as required and ensuring all are functioning and easily available for use.
- Keeping inspection and maintenance records.
- Familiarizing employees with laboratory hazards (use, handling, storage and transportation of equipment and agents).
- Completing an incident report for every incident and near misses. Situations to report range from unharmed minor cases like spills to major events requiring emergency equipment usage.
- Designating substitute supervision in the absence of the laboratory supervisor.
- Providing training for new employees and ensuring the training is completed before starting work. Training must be documented (e.g., by signed acknowledgment of training from employees), and must include WHMIS and any other required work with employee responsibilities.
Employee-Supervisor Checklist
The New Employee Orientation Checklist (PDF) needs to be filled out by the new employee and principal investigator (or appointed supervisor) together, and a copy must be forwarded to the safety officer, Chris Vogels (cvogels@mta.ca), within the first two weeks of being in the lab.
Lab and studio employees’ responsibilities
- Following the NB OHS regulations.
- Co-operating when taking the required training for your laboratory and ensuring all required training has been completed before starting the related lab work. WHMIS and understanding SDS is mandatory.
- Using PPE when performing activities that necessitate them.
- Always following label instructions, SDS, and working in a safe manner.
- Labelling all workplace containers when a substance is being transferred or created.
- Respecting the rules and safety procedures outlined in this manual and the laboratory’s specific work practices and safety protocols.
- Reporting all incidents, near misses, and potentially dangerous conditions to their supervisor.
- Consumption of food and drink in a lab or studio is strictly prohibited. Store and consume all food and beverages only in specified areas outside of laboratories and studios.
Visitor responsibilities
All visitors to Mount Allison’s laboratories and studios are required to:
- Obtain permission from the PI before entering.
- Dress in accordance with the laboratory requirement (e.g., closed shoes, tie back long hair, etc.) and wear PPE when required.
- Enter laboratories only when appropriately accompanied by a supervisor or lab employee who would oversee their safety.
Service animal owner responsibilities
Individuals who wish to enter laboratories with their service animal must co-ordinate with the Meighen Centre and have appropriate PPE for the animal as required. Assessment of the risks to the service animal, people in the lab, and the research are evaluated on a case-by-case basis.
3. Basic safety
Safety is the most important factor in any laboratory, and all personnel rely on appropriate behavior to maintain a safe working environment. Individuals working in the Chemistry and Biochemistry facilities should refer to the Laboratory Rules (PDF) for basic safety directed at that department, available on Moodle under “All courses > Safety Training & Lab Techniques > Lab Safety Training”.
Lab dress and footwear
The requirements outlined below will vary between laboratories based on the type of work that can be undertaken and the chemicals present in the workspace.
- Wear proper laboratory attire (e.g., lab coat, long pants, confine loose clothing and accessories).
- Wear shoes that cover your feet (no open-toed shoes).
- Tie back long hair.
In all labs:
- Use PPE as required.
- Eye protection meeting ANSI Z87.1+ and CSA 94.3 must be worn when performing procedures that necessitate their wear.
- Always remove lab coats, eye protection, gloves, and other forms of PPE when leaving a laboratory, even if you will be re-entering shortly (e.g., restroom, water break). If your PPE is intended to protect you from what you are working with, leaving it on will expose people in public spaces to the hazards you are protecting yourself from. Alternatively, if your PPE is intended to protect your work from you (e.g., when working with DNA or RNA), people in the hall will not know that this is the case and will be left worrying about what you might have exposed them to.
Unattended procedures
Whenever possible, processes in a lab should be completed during normal working hours (8:30 a.m.–4 p.m.). However, it is recognized that not all experiments can be completed during this time.
- Any processes that may be left unattended should be reviewed between the supervisor and employees. All potential hazards should be considered before being approved to run unattended. Before running a procedure unattended, a sign with the date and time of initiation and expected completion should be indicated, as well as the name and contact information of the person responsible for the procedure.
- Unattended procedures should be checked regularly during their process.
- Systems that require cooling water systems should not be used unattended.
Working alone
Occasionally individuals may be required to work after hours (between 4:30 p.m. and 8:30 a.m., weekends, and University holidays) or alone in laboratories.
Additional measures are required to ensure one's safety. Following provincial and federal legislation, supervisors need to assess the risks of completing a procedure after hours or alone.
An employee must have previous experience with the procedure before carrying it out alone. It is the supervisor’s responsibility to ensure that employees working alone adhere to WHMIS standards and other safety policies and are familiar with emergency procedures.
Supervisors have the right to deny employees permission to work after hours or alone. For additional information please visit Faculty of Science Policy for Working Alone and/or After Hours.
Individuals are required to complete the Permission to Work Independently Form (PDF). If the individual does not have their form completed and with them during after-hours or while working alone, campus security will make them exit the building.
Individuals will need to have read the Faculty of Science Policy for Working Alone and/or After Hours and have reviewed it with their supervisor.
An individual working alone or after hours is required to state which laboratory they are in, and check in and check out with their supervisor. This includes setting a check-in progress interval, e.g., every hour. If the contacted person does not hear from the individual within the time planned, they should contact campus security [(506) 364-2228] and ask them to check on the individual and call them back.
Housekeeping
- Lab benches and other work areas must be kept clean and tidy after activities are completed or at the end of the day.
- Doorways, stairwells, walkways, emergency exits, and equipment must always be free of obstructions. It is prohibited to place laboratory equipment or personal belongings such as bikes and bags in such location.
- Chemical spills must be handled immediately. Depending on the risks associated with the chemical, it must be cleaned up if safe to do so. Contact Philip Cormier (pcormier@mta.ca) for assistance. See information on hazardous chemical spills under section 12 — Emergencies.
- Plastics, sharps, broken glassware, chemical and biohazard waste must be dealt with appropriately and placed in their rightful waste containers. See information on glassware under section 3 — Basic safety.
- Unlabelled or expired materials must be disposed of immediately to prevent their accumulation, which is deemed unsafe. Contact Philip Cormier (pcormier@mta.ca) to arrange a disposal time.
- Corrugated cardboard must be broken apart and placed in the hall when disposing for most buildings, unless a designated disposal area for cardboard exists (e.g., ground floor loading dock in Purdy Crawford Centre for the Arts).
- For large items contact Facilities Management (fixit@mta.ca) before placing them in the hall.
- Flammable waste (such as used oil paint or solvent in the case of Fine Arts) must be disposed of in a flame-proof can with a self-closing lid.
Lab equipment maintenance
A qualified person must undertake the inspection and maintenance of laboratory equipment. The frequency of inspection is determined by the manufacturer’s instructions, regulations, or the hazardous risk associated with the equipment. The laboratory supervisor is responsible for keeping inspection and maintenance records.
Glassware
- If glassware is chipped, cracked, or would not handle the normal stressors, do not use it.
- Discard or repair by a professional all damaged glassware.
- Use a brush and dustpan to pick up broken glass, do not pick it up with your hands, and ensure proper footwear is worn.
- To discard broken glass, place it in a rigid container labeled “Broken Glass” — do not place it in the regular garbage.
- Everyday stresses such as heating and bumping can weaken glass — extra care must be taken when handling used glass.
- Glass that is subject to high pressure or vacuum must be protected. To minimize risks of glass vessels projecting, wrap cloth tape around or use appropriate shielding.
- Contaminated glassware must be handled as hazardous material, see information on hazardous waste and disposal in section 4 — Chemical safety.
- Hot glass does not look any different from cold glass. Exercise with caution when handling hot glassware. Use thermally rated gloves.
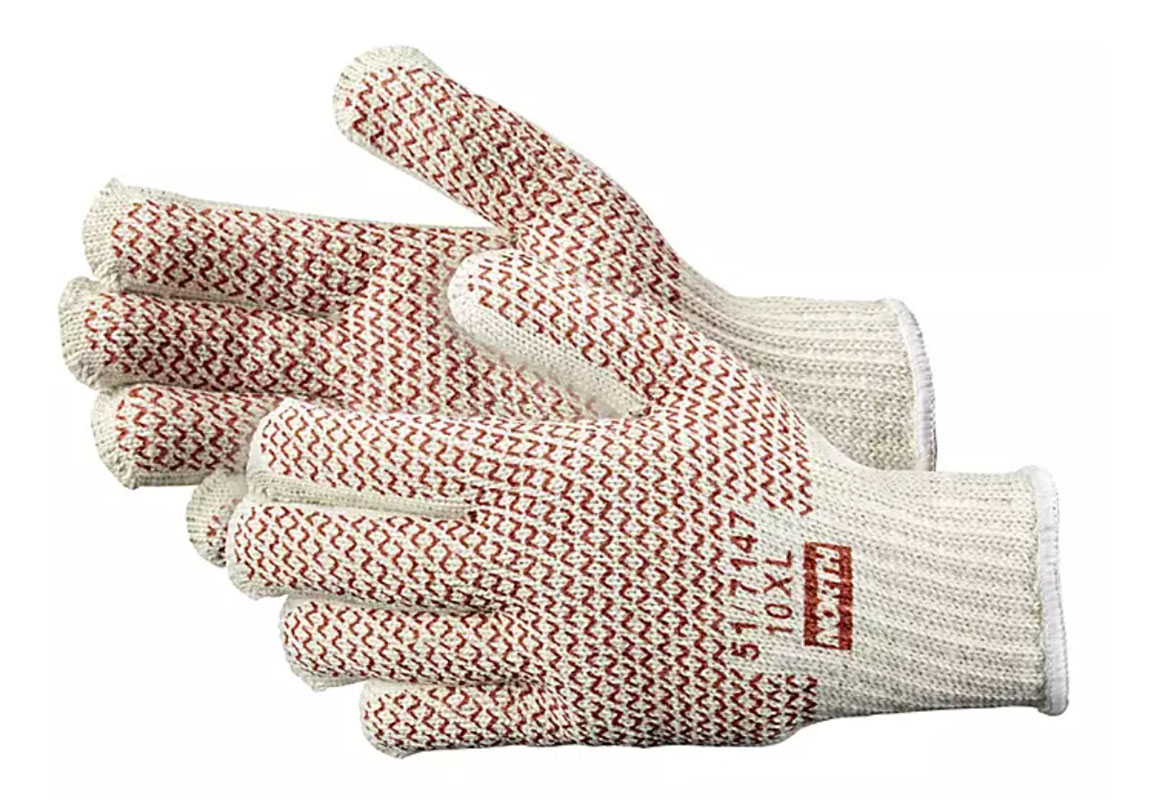
Guarding
Under the General Regulation — NB OHS Act 242(1), where an employee may come into contact with moving drive or idler belts, rollers, gears, driveshafts, keyways, pulleys, sprockets, chains, ropes, spindles, drums, counterweights, flywheels, couplings, pinch points, cutting edges or other moving parts on a machine that may be hazardous to the employee, an employer shall provide adequate safeguards to prevent such contact.
Mechanical equipment can pose a risk if electrical connections and moving parts are not appropriately guarded. For instance, centrifuges must have an inner lock while the machine is running to prevent injury from attempting to open it. Any attempt to defeat such safeguarding is prohibited.
Shielding
Shielding is the placement of a physical barrier between a worker’s body and a hazard that could cause injury. Shielding is required when a procedure involves:
- Chemicals or materials that may have explosive or splashing risks.
- When a new procedure is attempted.
- When a familiar procedure is carried out on a larger scale than previously done.
- When using different conditions than usual.
- For procedures that may experience thermal hazards.
- When involving corrosive materials.
- For procedures involving non-ionizing radiation and magnetic sources such as microwave radiation, UV, infrared, and lasers.
At Mount Allison shielding is usually achieved by conducting work in a fume hood with the sash lowered. If this type of shielding does not work, contact Philip Cormier (pcormier@mta.ca)
4. Chemical safety
Workplace Hazardous Materials Information System (WHMIS) used in Canada is an information system on safely handling hazardous products in the workplace. This information is provided as an education program and in the form of Safety Data Sheets (SDS). Federal and Provincial laws and regulations, Hazardous Products Information Regulation (S-2.1, r.8.1) and Act Respecting Occupational Health and Safety (AROHS) (R.S.Q., c. S-2.1) make up WHMIS.
At Mount Allison, all students, faculty, staff, and visitors to laboratories that have hazardous materials are required to complete the WHMIS training. This training can be completed on Moodle in a self-enrolled class called WHMIS Lab Safety Training. If you have completed your training but need more information refer to WHMIS 2.0 (PDF) available on Moodle under “All courses > Safety Training & Lab Techniques > Lab Safety Training”.
Safety Data Sheets (SDS) are associated with each hazardous product and contain emergency, handling, and safety information as well as chemical, physical, and toxicological properties.
- SDS must be in every laboratory and be easily accessible to everyone as a paper copy.
- SDS must be renewed when an updated version becomes available by a hazardous product supplier. The laboratory supervisor is responsible for ensuring the newest version is available.
- Laboratory supervisors are responsible for maintaining an updated inventory of the hazardous products in their labs and their corresponding SDS.
Transporting chemicals on campus
When transporting chemicals to another laboratory or across campus, follow the guidelines below:
- Label chemical with the product’s name and originator’s name.
- Carry in a secondary container. Secondary containers can be borrowed from ScienceStores (Room 08 Barclay Building).
- It is advised to carry two chemicals at a time and make multiple trips as needed or use a cart.
- If using a cart with a flat top, place chemicals in a polypropylene tray on the cart, and ensure the chemicals placed in the same tray are compatible.
- Take extra care when moving between buildings, e.g., the quad and outdoor stairs may be slippery.
Transporting chemicals to off-campus worksite
Transportation of chemicals to off-campus sites can be needed for field work and for accessing other facilities.
- University vehicles (including vehicles rented under MtA insurance) should be used for transporting chemicals, using private vehicles is prohibited.
- Cryogenic chemicals should be transported in an open vehicle, e.g., in the back of a pickup truck.
Regulations for transportation will vary with the chemicals in question, consult federal transportation regulations prior to transporting.
Chemical storage guidelines
- Chemical storage should be kept to a minimum. Do not buy volumes larger than four litres at a time.
- Arrange with ScienceStores (Room 08 Barclay Building) for obtaining bulk purchases and quantities smaller than available.
- Heavier liquids should be stored on lower shelves and frequently used liquids should be stored between hip and shoulder level.
- Ensure shelves capacity can withhold the weight of the stored chemicals.
- To determine how a chemical should be stored, consult the SDS.
- Flammable and combustible chemicals should be stored in a flammable cabinet. See section 5 — Flammable and combustible materials.
- Corrosive materials should be stored according to compatibility in a corrosive cabinet. Acids and bases must be stored in separate corrosive cabinets. Storing corrosive materials in secondary containers in addition to the manufacturer’s container is advised. See information on storing corrosives in section 6 — Corrosive materials (including acids and bases).
- Substances that need to be stored in the cold should be placed in a designated fridge where other materials unrelated to research or teaching are prohibited. The fridge must be labeled “NO FOOD OR DRINK”.
- Some chemicals have explosive properties after their expiry date. These chemicals require regular checking and must be disposed of before the expiry date. If an expired chemical is found, do not touch it and contact Chris Vogels (cvogels@mta.ca).
- For additional information about chemicals that need prior approval, contact Chris Vogels (cvogels@mta.ca).
- Never store any chemical or samples in a refrigerator that is used for food.
- Solutions that contain more than one chemical must be stored in an appropriate container that is compatible with all components of the solution.
- Containers must be labelled with the product name and information on how to handle the product safely, for each chemical. It should also state that an SDS is available (an associated SDS is required). WHMIS training is required.
- Helpful tip: Name of the person who prepared the solution and the date prepared can be added to labels.
Hazardous waste and disposal
- Chemicals that cannot or will no longer be used, need to be collected and disposed of appropriately.
- For disposal of chemicals please contact Chris Vogels (cvogels@mta.ca). Do not wash any chemical down the sink.
- Do not fill waste containers more than 90 per cent capacity to allow for solvent expansion.
- Empty clean containers can sometimes be re-used as waste containers; however they must meet the following criteria:
- The material that makes up the container should be compatible with the waste that will be added.
- The containers' previous content should be compatible with what will be added, in case residue from the original substance remains.
- The seal of the container should be well-fitting and not damaged.
- The container must be in good condition, leakproof, and sturdy.
- For assistance, contact Chris Vogels (cvogels@mta.ca).
- All waste containers must be labelled with an appropriate hazardous waste label that includes the contents of the container, date of initial addition of waste, contact information of the originator and special handling information if needed. Chris Vogels (cvogels@mta.ca) should be contacted for label acquisition.
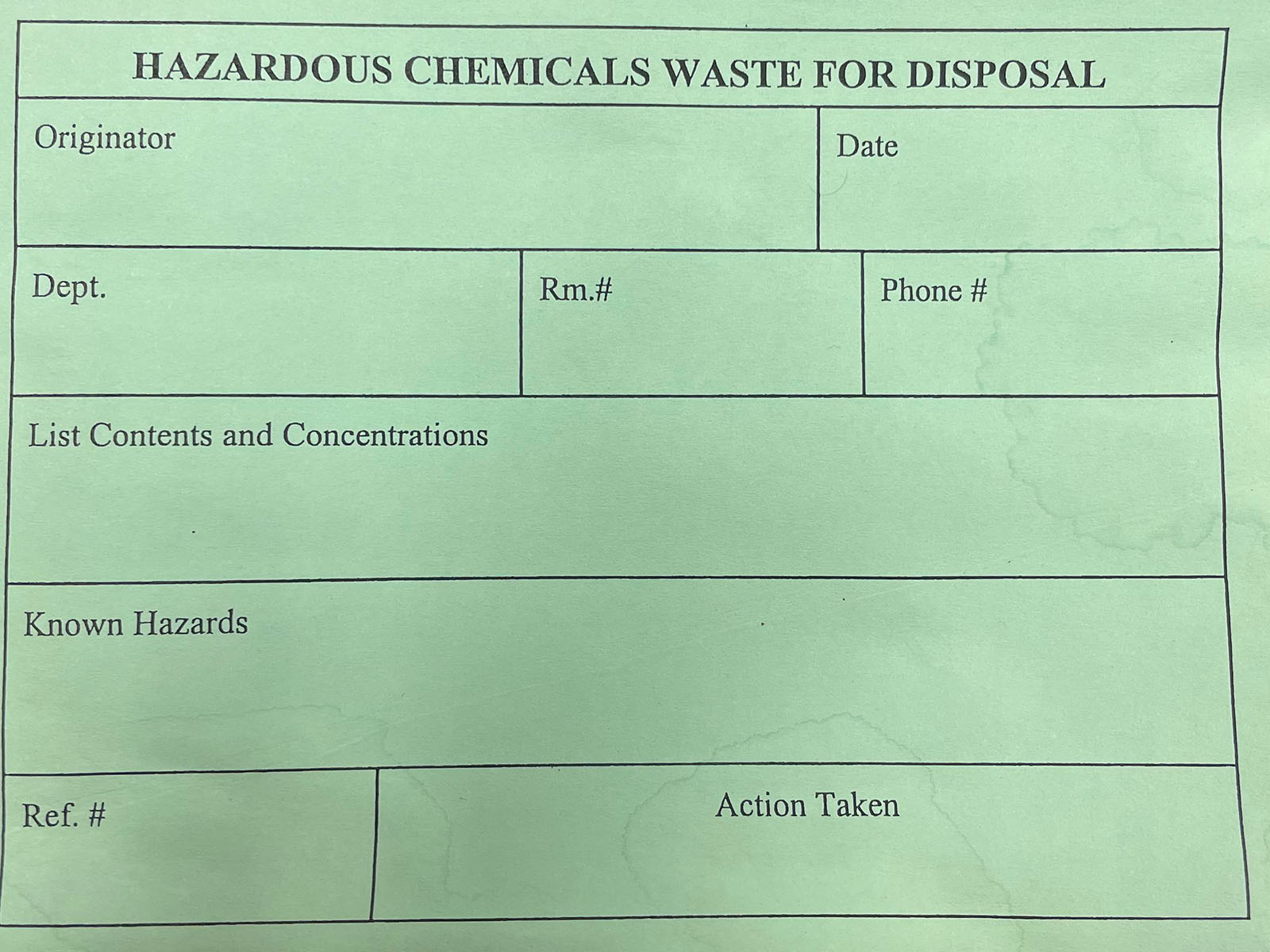
Procedure for waste disposal
- Attach the hazardous waste form to all containers
- Fill out the attached waste form as described in the Excel file. (Click 'show comments' for additional information.)
- Send the Excel file to pcormier@mta.ca for processing
- You will receive the Excel file back with the generator number.
- Place the number on the hazardous waste form.
- Arrange a time (Monday/Wednesday/Friday 8:30 a.m.–10 a.m.) to bring hazardous waste to ScienceStores (Room 08 Barclay Building).
Note: you can bring contaminated gloves, plastics, and hydrocarbon/halogenated waste without filling out this form. This is only for specific hazardous waste originating from labs (purchased or produced).
5. Flammable and combustible materials
Flammable materials can ignite at room temperature when exposed to sparks or heat. Combustible materials can ignite when heated. Keep flammable and combustible materials away from open flames.
- Notify others if working with such materials.
- Use fume hood when working with flammable or combustible solvents.
- Only use lab equipment when heating flammable materials.
Such materials should be stored in a flammable cabinet with the following specifications:
- Use only a certified flammable cabinet.
- Minimize quantities stored.
- Cabinet doors must remain closed when not in use.
- Flammable cabinet must be in a well-ventilated space.
- Flammable material should be stored separately from substances that may react to create a hazardous condition, such as liberating toxic or flammable gas.
- Flammable waste (such as used oil paint or solvent in the case of Fine Arts) must be disposed of in a flame-proof can with a self-closing lid.
6. Corrosive materials (including acids and bases)
Hazardous nature of corrosives
Corrosives (e.g., acids, bases, chlorine, ammonia) are materials that can damage body tissues if inhaled or ingested, or when put in contact with skin directly. They can react with other chemicals and materials which can impose additional risks (e.g., flammable hydrogen gas may be released from metal damaged by corrosives).
- Corrosives must be stored in a corrosive cabinet and sorted into separate cabinets according to compatibility. Chemicals stored together should be compatible. Acids and bases must be stored in separate corrosive cabinets.
- Secondary containers should be used when transporting corrosive materials.
- SDS may state additional special storage requirements.
Diluting acids and bases
- Dilute acids and bases in a fume hood.
- Always dilute acids or bases by adding concentrated solutions to water and mixing slowly, never add water to the acid or base. “Add the Acid” is a helpful mnemonic device.
- NEVER ADD WATER TO CONCENTRATED ACID SOLUTIONS.
- Adding acid (or base) to water is important because such reactions are often exothermic, and the created solution could heat up to near boiling. Adding the acid (or base) while mixing ensures that concentrations at initial contact between acid (or base) and water are weak.
- Mixing strong acid and strong base produces violent reactions.
- In all procedures using acids and bases, the weakest possible concentration should be used.
General precautions for working with corrosives
- Always read and follow the information on SDS.
- Handle all corrosive materials in a fume hood.
- Always wear goggles.
- Always use appropriate gloves (can change depending on the corrosive).
- Dilute by adding acids to water (“Add the Acid”).
- Use the weakest concentration possible.
- Secondary containers need to be used when transporting corrosive materials.
- Clean up after use.
- Some corrosives like Picric acid and Hydrofluoric acid have special guidelines for handling.
- Locate spill kit and eyewash station in case of emergency before starting work with corrosives. If you need additional information, contact Chris Vogels (cvogels@mta.ca).
Spills involving corrosives
If you have not been trained to clean spills or the spill cannot be cleaned up (spill is greater than 250ml, you are uncertain on how to proceed or in fear) evacuate the room and contact Chris Vogels [(506)-233-8588]. See information on hazardous chemical spills in section 12 — Emergencies.
7. Cryogenic materials
Cryogenics are materials that have very low temperatures such as liquid nitrogen and liquid helium.
Cryogenic training is required to dispense or work with cryogenic material. To complete cryogenic training or if you have completed your training but have questions, refer to the Cryogenic Plant Safety Manual (PDF) available on Moodle under “All courses > Safety Training & Lab Techniques > Lab Safety Training” and contact Chris Vogels (cvogels@mta.ca).
8. Ventilated engineering control
Purpose of a ventilated engineering control
Ventilation engineering control replaces air in the work environment, as such, it provides a continuous supply of fresh outside air and removes or dilutes air contaminants.
Types of ventilated systems and what type of work is done in them
Fume hood is a closed off unit with a sash that slides to open and close the hood. Fume hoods should be used when working with chemicals that can emit hazardous vapors. Spills can be contained, and risks minimized if occurring within a fume hood. Whenever possible work in a fume hood. Chemicals that must be handled in a fume hood can be identified by looking at their SDS. Chemicals should be used in a fume hood if SDS mentions dangerous vapours, dust, inhalation warnings, or if mechanical ventilation is listed under PPE requirements.
Flow cabinet uses ventilation through a HEPA filter to trap contaminant particles that would otherwise affect the product or the experimental process. A flow cabinet does not protect the user from hazardous materials. It should be used when carrying out experimentation that needs to be protected from contamination.
Spray booth is a power-ventilated structure provided to enclose or accommodate a spraying operation to confine and limit the escape of spray, vapour, residue, and to safely conduct or direct them to an exhaust system (OSHA 1910.107(a)(3)). Aerosol paints, adhesives, and fixatives are examples of common materials in Fine Arts that must be used in a spray booth.
Local exhaust ventilation is installed alongside specific equipment and work surfaces where hazardous vapours or particulate may be generated. This type of ventilation is designed to capture contaminants at or near the source and exhaust them to a safe emission point, often outside. Local exhaust ventilation is present in Fine Arts studios including sculpture, photography, and printmaking. In some cases, the ventilation is engineered to run constantly (i.e. photography darkrooms). In other cases, the ventilation must be turned on manually (i.e. before using power tools in sculpture).
Allowable storage
- Materials should never be stored for longer than a day inside the fume hood and spray booth.
- It is preferred to only keep material inside the hood while the experiment is ongoing as air flow disturbance can occur from clutter.
Sash height
- During use, the sash should be put as low as workable.
- When not in use, the sash should be kept closed with the fume hood always running.
- Some fume hoods can be turned off. If a fume hood is turned off, it should be locked.
Maintenance
- Evaluate fume hood condition before each use and at least once a month.
- Ensure no lightweight material (e.g., paper, aluminum) or dust are obstructing airflow in the fume hood.
- An air flow monitoring device should be inspected before each use to ensure sufficient air flow.
- Annually, fume hoods must be assessed and documented by Facilities Management (fixit@mta.ca).
- During any fume hood repair, the supervisor must ensure the fume hood is clean and all chemicals have been removed from the hood and from underneath it.
Alarms
If low flow is indicated or the fume hood alarm switches on, stop working and close open chemicals and the sash. Immediately contact your lab supervisor and Facilities Management (fixit@mta.ca). Do not use fume hood again until repaired or until the problem has been addressed.
Other fume hood precautions
- Chemicals in the fume hood should be elevated whenever possible to prevent vapours from escaping in the laboratory.
- Chemicals and equipment inside the fume hood should be distanced at least 15 cm away from hood opening.
- Work as far away from the sash as reasonably practical.
- You may pass your head through the fume hood when setting up, but once the set-up is in place, do not pass your head through the sash.
9. Compressed gas
Compressed gases can be used to carry out unique chemistry, for instance experimentations under atypical atmospheric conditions.
For more information on storage, safety handling, transportation, refer to the Compressed Gases Manual (PDF) available on Moodle under “All courses > Safety Training & Lab Techniques > Lab Safety Training” or contact Chris Vogels (cvogels@mta.ca).
10. Autoclaves
Autoclaves use high pressure and temperature to decontaminate equipment from microorganisms, spores, DNA, RNA, etc. It is mandatory to complete autoclave training before attempting to use or touch an autoclave. For training or for further questions on autoclaves, please contact Shelley LeBlanc (shleblanc@mta.ca).
11. PPE and safety equipment
Personal protective equipment must be worn when working with hazardous products.
Gloves
Gloves protect your hands from chemical products, physical damage, extreme temperature, and protect samples from contamination (e.g., from your DNA). The proper glove to wear will depend on the risks associated with the materials you are working with, this can be identified on SDS, protocols or as directed by your supervisor. Refer to the Glove Manual (PDF) available on Moodle under “All courses > Safety Training & Lab Techniques > Lab Safety Training > Glove Manual” for more information on glove selection and how to handle and remove gloves safely.
General glove handling includes:
- Never re-use a disposable glove.
- Contaminated gloves should be disposed of accordingly (based on SDS of the contaminant).
- Do not touch electronic equipment or personal belongings with gloves (e.g., computer, phone).
Be aware, latex gloves can cause skin reactions for some people. If skin reaction occurs from its use, alternatives exist such as non-latex and nitrile gloves.
Eye protection
Eye protection meeting ANSI Z87.1+ and CSA 94.3 is required to be worn under the following circumstances:
- Areas where hazardous products are being worked or stored.
- Areas where prone to eye hazards such as UV (additional UV protection required).
- Areas where substances could splash, or objects be ejected (goggles with face shield required).
Skin protection
When handing hazardous materials, appropriate protective clothing such as lab coats and rubber aprons must be worn. Refer to SDS for clear PPE requirements. In general:
- Lab coats should have snap closures and elastic cuffs.
- Coverage from clothes worn in a laboratory should be maximized based on the substances one will work with.
- Rubber aprons must be worn when performing special procedures of large quantities (e.g., transferring corrosives and cryogenics).
- When working with highly toxic substances, wear a hard front coat which closes at the back.
- A leather welding jacket and leather gloves must be worn when using welding equipment in the sculpture studio to protect the skin from reflection and burns. Protective clothing should be removed when leaving the laboratory or if potential contamination is present on the clothes.
Respiratory protection
In addition to ventilated engineering controls, a mask or respirator may be required when handling materials that pose a respiratory hazard. Select the type of mask or respirator cartridge in accordance with the hazard (particulate, organic vapour, etc.) in consultation with the SDS.
Eyewash and emergency shower
- If eye contamination or suspected contamination occurs, an eyewash station should be used immediately. If contamination of any body part occurs or is suspected, an emergency shower should be used.
- Eyewash stations should be tested weekly for at least one minute.
- If you need more information on usage and maintenance of eyewash stations, contact Chris Vogels (cvogels@mta.ca).
- Any incident requiring use of an eyewash or emergency shower must be reported to the Health and Safety Committee (fasjhsc@mta.ca). Contact your supervisor and Chris Vogels [(506) 233-8588] or your departmental representative.
12. Emergencies
Never hesitate to call 911 in an emergency.
Report all near misses, incidents, and spills
Any event causing harm to person or property, and any “near miss” event that could have caused harm to person or property must, by law, be reported to the Health and Safety Committee, no matter how small the event might seem.
The Committee is responsible for investigating the event. The goal of incident investigation is not to assign blame. Instead, the goal of investigation is to identify underlying causes and to suggest modifications to prevent similar events in the future.
Emergency phone number
Every laboratory should have relevant emergency phone numbers posted. This includes laboratory supervisors, PI, facilities management, Chris Vogels, campus security, and emergency services (e.g. ambulance, fire). The posting should have the address of the exact location of the laboratory and building to inform services in an emergency.
Emergency equipment
- There should be an adequate number of appropriate types of fire extinguishers for materials found or produced in the corresponding laboratory.
- At all times, eyewash stations and emergency showers must be accessible for use. An individual must not have to travel more than 10 meters or have to go through more than one door to access such equipment.
- If you need more information on spill kits, contact Chris Vogels (cvogels@mta.ca)
First aid
- All laboratory workers must know the nearest location of a University-designated first aid kit — this is to be ensured by the laboratory supervisor.
- Every first aid station must have a designated first aider. It is recommended to have the first aider’s contact information and where they can normally be found posted at the first kit station. For more information, see first aid providers and equipment location. If a designated first aider cannot be found, call 911.
- Laboratory supervisors can provide their own supplementary first aid kit. This does not replace the designated first aid kit and all incidents should be handled by the designated University first aid provider for that space.
- All first aid intervention must be reported to the Health and Safety Committee (fasjhsc@mta.ca)
- It is recommended that first aid interventions such as skin and eye exposure be followed by a consultation with a physician.
Skin exposure
- If the exposure affects a large area of the skin, an emergency shower should be used. If exposure affects a small area, the nearest drench hose can be used.
- Skin should be flushed for 15 minutes or as indicated by SDS.
- Contaminated clothing should be removed once skin is under running water.
- Soap should not be used unless stated otherwise on SDS.
- If the skin was contaminated with a hazardous product, call 911.
- If an individual is taken to the hospital or to a physician, ensure the appropriate SDS goes with them.
- If you need more information, contact Chris Vogels (cvogels@mta.ca).
- Abundantly run water to the open eyes (hold eyelids open to help) at an eyewash station for 15 minutes or as stated in SDS.
- Remove contact lenses as quickly as possible after eye flushing has begun.
- While the water is flushing, run your eyeballs around to rinse the entire eye surface.
- If the eyes were contaminated with a hazardous product, call 911.
- If you need more information, contact Chris Vogels (cvogels@mta.ca).
Hazardous chemical spills
If the chemical spill is of a hazardous product, the following must be done:
- Take immediate action to prevent further release of the material. This may include stopping the source of the leak, containing the spill with available material, or removing sources of ignition if the spilled material is combustible.
- Report the leak or spill to Facilities Management [(506) 364-2444] or Campus Security [(506) 364-2228]. In the Barclay Building, contact Chris Vogels [(506) 233-8588].
- If you have any concerns about your safety or that of others in the area, evacuate the area immediately, close the door behind you, activate the fire alarm, and evacuate the building using the University's evacuation procedures.
- Move 100 meters away from the building and meet the Sackville Fire Department and/or Facilities Management staff to provide information on the leak.
- Do not re-enter the building until advised it is safe to do so by first responders or University staff such as the building warden, members of the security team, or Facilities Management staff.
- Perform first aid if needed.
- Do not attempt to clean the spill unless trained to do so.
- If trained, use SDS to assess if the chemical spill and area is safe for you to handle the spill.
- Ensure the air exhaust machine is turned on.
- If the chemical spilled is flammable, switch off electrical source in that area (if possible).
- Contact the laboratory supervisor to determine how the situation should be handled.
- Use the required PPE and any special agents as directed by SDS. If you need more information on spill kits, contact Chris Vogels (cvogels@mta.ca).
- Report the incident to the Health and Safety Committee (fasjhsc@mta.ca).
Exposure to certain chemicals may require decontamination, quarantine, and/or medical attention. Seek instruction from first responders and/or Facilities Management staff.
Laboratory fires
Fire to clothes: If your clothes are on fire, stop where you are, drop to the floor, and roll to suffocate the flames. Do not run, as additional air would support the flames. Once the fire has been put out, the individual must go to an emergency shower to cool off burns and 911 should be called.
Fire to laboratory area: A major way of preventing fires is to know the potential fire hazard of the chemical you are using by referring to the SDS and work with appropriate equipment such as sealed heating sources (e.g., hot plate). Never use an exposed heating element with flammables (e.g., Bunsen burner).
You can attempt to put down a fire if comfortable using a fire extinguisher; if not follow these steps:
- Activate the nearest fire alarm.
- Leave the fire scene, help anyone you can if possible.
- Evacuate the building using stairs in an orderly fashion. Do not use the elevator and move away from the exit to allow others to leave the building easily. Each building has its own fire evacuation plan.
- After you have left the building, report the nature of the fire, associated hazards of the fire, evacuation route, and individuals in need of assistance to the fire wardens and Facilities Management [(506) 364-2444]. For more information, visit our what to do in an emergency page.
- If your building is evacuated for a fire or other emergency, you should go to the designated assembly area for your building.
Report all burns and fires even if extinguished by you to the Health and Safety Committee. (fasjhsc@mta.ca)
All depleted fire extinguishers must be replaced immediately, contact Facilities Management (fixit@mta.ca).
13. Electrical safety
Electricity can present both shock and arc flash hazards.
Shocks
Shocks occur when there is a path from high electrical potential to low potential through your body, leading to electric current flowing through you. The severity of the shock depends not only on the amount of current (governed by the voltage difference), but also the duration of the shock, the path taken through your body, and the amount of moisture on your skin. Typically, shock currents of approximately 1 mA will lead to a mild sensation, 9 mA will be painful, 16 mA will cause muscle contractions, and 100 to 1000 mA currents are life threatening.
Arc Flashes
Arc flashes occur when current leaves its intended path and arcs through the air, leading to a violent explosion with intense heat. Arc flashes can be caused by many things including dust, corrosion, condensation, material failure, and accidental contact. The severity of injury due to an arc flash depends on your proximity to the hazard, the short circuit capacity of the circuit, and the time before the breaker or fuse trips and cuts off the circuit.
Personal Protective Equipment (PPE)
If you are working with circuits that are OPEN, EXPOSED, and LIVE, then you must wear the appropriate PPE. When these conditions are true, voltages above 30 VAC or 60 VDC require:
- Appropriately rated rubber gloves for shock protection
- Thermally protective clothing that limit the incident energy on skin to less than 1.2 cal/cm2
- Thermally protective face shield
- Ear protection
Working with voltages 30 VAC or 60 VDC or below do not require PPE. This means circuits at these low voltages can have open, exposed connections and be handled safely even when live.
In this context, OPEN means the circuit is not fully enclosed in a protective casing. If you can see the wires and circuit components, then your circuit is open. Most custom-built circuits used in the lab will be open.
EXPOSED means that there is bare conducting material that could touched by a person or a tool. In a lab where you have a custom-built circuit, alligator clips would be considered exposed whereas banana plugs fully inserted into the appropriate socket would not.
LIVE means the circuit is powered on. Another term for this state is energized.
Additionally, if the circuit or enclosure is in an abnormal condition (e.g. due to rust or cracked insulation), then appropriately rated PPE should be worn.
Below are two images of circuits that are OPEN (their wires and components are accessible) and EXPOSED (there is bare conducting metal), but are not LIVE because they are not plugged in.
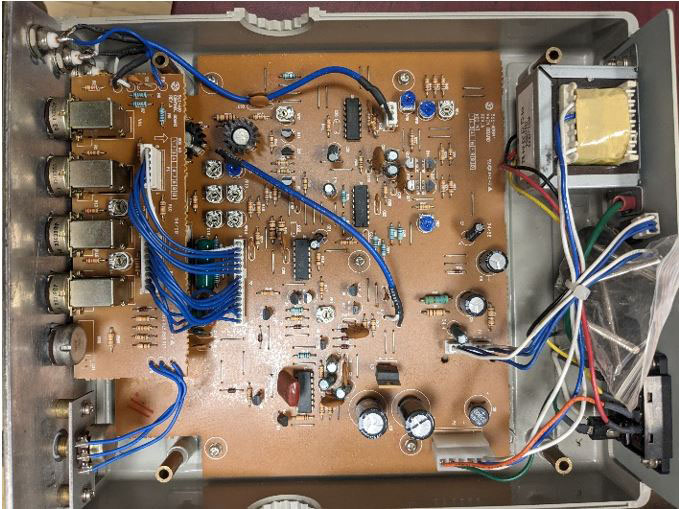
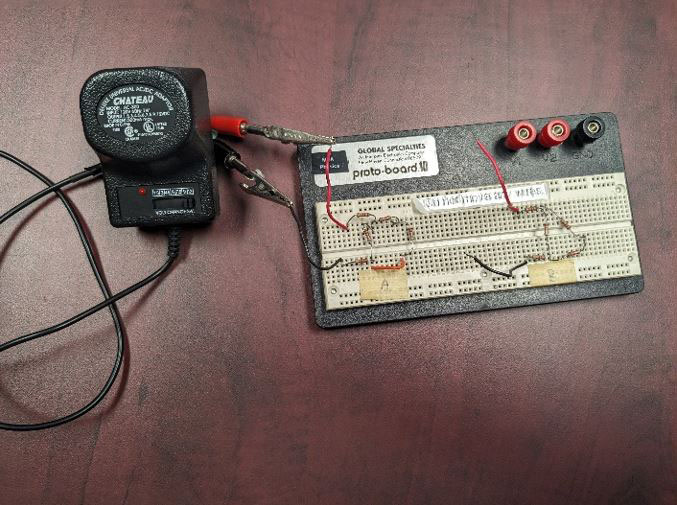
Arc Flash, Limited Approach, and Restricted Approach Boundaries
If working with voltages greater than 30 VAC or 60 VDC, and with a circuit that is open, exposed, and live, an arc flash assessment must be done before-hand by a qualified, trained professional to determine safety boundaries for the following zones (listed from largest to smallest):
- Arc Flash Boundary inside of which appropriate arc flash PPE must be worn.
- Limited Approach Boundary inside of which untrained individuals must be accompanied by a qualified and trained professional.
- Restricted Approach Boundary inside of which appropriate shock protection must be worn.
Medium and High Voltages
Any work with voltages greater than 300 V is considered medium voltage and greater than 750 V is considered high voltage. In either case:
- A warning sign must be displayed indicating the potential hazards.
- The room should be locked when not in use to limit general access.
- At least two people must be present in the room.
- A First Aid Responder trained in CPR must be available in the building.
Ground Fault Circuit Interrupters (GFCI)
Ground Fault Circuit Interrupter (GFCI) outlets work by detecting loss of electrical current in a circuit (e.g., it will trip when current flows through your body instead of the circuit). When a loss is detected, the GFCI turns the current off before severe injuries can occur. A painful non-fatal shock can still occur during the time that it takes for the GFCI to cut off the electricity, so it is important to use the GFCI as an extra protective measure rather than a replacement for safe work practices.
GFCI outlets must be used within 1.5 m of a water source such as a sink to counteract the increased risk of electrocution from the water. Wet skin is much more conductive than dry skin, and so it is much more likely to have dangerous current levels pass through you if you are wet or damp.
Additionally, always use a GFCI when using portable electric tools outdoors or in damp or wet locations.
Best Practices
- Always check electrical equipment for excessive dust, corrosion, or damage to the insulation. Do not operate if not in good working condition.
- If equipment is not in good working condition, label with a sign or sticker saying “Broken - Do Not Use” as well as a brief, one-line description of what the issue is. Inform your supervisor as soon as possible; they may need to follow lock-out/tag-out procedures if the device could cause harm when energized.
- Do not modify or alter a circuit while it is energized. Always shut the power off first.
- Properly insulate connections so that no conducting material is left exposed. (Not necessary for circuits at voltages less than 30 VAC or 60 VDC e.g. like those built on a bread board.)
- Always use meters appropriate to the current or voltage to be measured. Using the wrong meter can cause an arc flash.
- When using a meter to check if a circuit is dead, use the Live-Dead-Live method. You first check that your meter is working by checking it with a known live source, then you check that the circuit of interest is dead, then finally re-check the known live source to make sure the meter did not break during the previous measurement.
- Do not plug several items into one outlet.
- Extension cords should only be used as a temporary measure, not a long-term fix.
- Do not daisy-chain power bars.
- Do not pull the cord to remove plug from outlet. This causes wear and leads to failure.
- Never remove the third prong (ground) from a plug.
- If you see someone being electrocuted, do not touch them. Instead, turn off the power to equipment.
- Contact your supervisor if any electronics feel excessively hot.
- Never use water to attempt to extinguish an electrical fire.
- Do not touch energized electrical equipment when it is wet.
Questions, comments, and concerns
If you have any question about the content of this manual, please contact the Fine Arts and Sciences Health and Safety Committee. (fasjhsc@mta.ca)